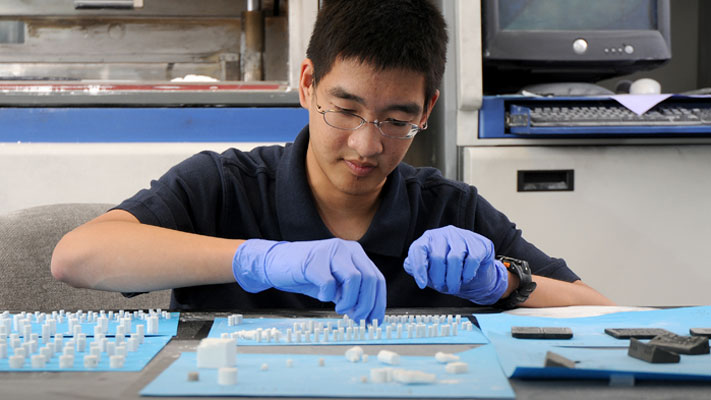
Kevin Wu works with tiny scaffolds made from bioactive glass powder. Photos by B.A. Rupert
This summer, eight undergraduate students from across the country have come to S&T for a solid research experience in additive manufacturing, a technique that constructs components in layers. The method can create complex 3-D shapes and produces far less scrap than conventional methods.
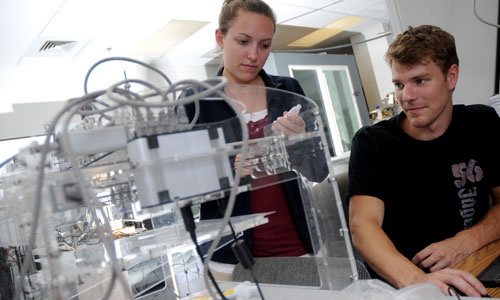
Maggie Bollinger and Brad Harris test 3-D printer.
The Additive Manufacturing Research Experiences for Undergraduates (REU) Program is funded by the National Science Foundation. Dr. Robert Landers, associate professor of mechanical and aerospace engineering, is program director. In its first year, the program is funded for three summer sessions.
The additive manufacturing methods researched by the students range from small printers geared towards home fabrication to large machines that use extreme temperatures to produce high-tech components.
Brad Harris, a senior in mechanical engineering at S&T, works with Maggie Bollinger on a 3-D printer that can make objects out of a variety of materials, including silicone, epoxy, gypsum plaster, and even frosting and cheese.
Bollinger, a junior from Virginia Tech, says she and Harris design an object on the computer, print it out using silicone gel, then test it to learn more about the printer’s limitations.
“There are all kinds of home applications for this,” says Bollinger. “You could make nose pieces for your eyeglasses, cooking utensils, or even Barbie shoes.”
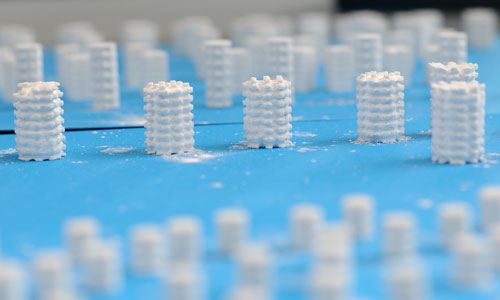
Rabbit and rat scaffolds.
Kevin Wu, a junior in materials science and engineering at UC Berkeley, works on a selective laser sintering machine, which heats powder until its particles adhere to each other. He builds tiny bone scaffolds made from bioactive glass powder, supplied by MoSci Corp., a glass technology company founded by Dr. Delbert E. Day, Curators’ Professor emeritus of ceramic engineering at S&T.
“These tiny scaffolds are for rats and rabbits,” he says. “They are designed to allow the bone to heal naturally. The material is porous and the cells stick to walls, allowing nutrients to flow through. The bone heals faster and the scaffold becomes part of the skeleton.”
Others work on a freeze-form extrusion fabrication (FEF) machine, which uses freezing temperatures to build ceramics capable of withstanding ultra-high-temperatures.
The students present their research findings weekly and will do a formal presentation at the end of the 10-week session.
By Linda Fulps
Recent Comments