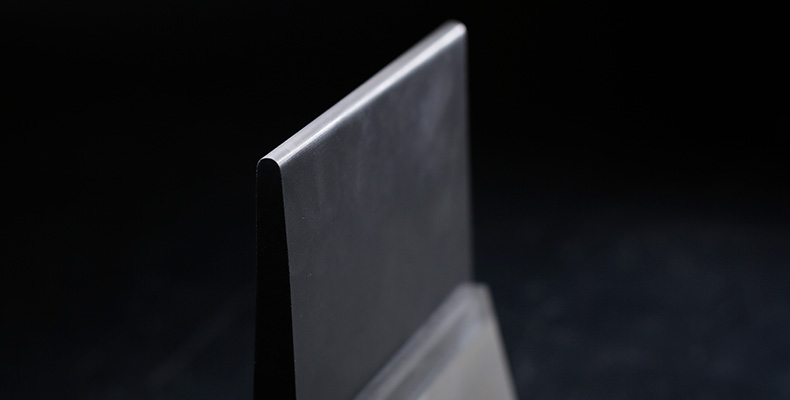
Missouri S&T researchers are investigating ultra-high-temperature ceramics like this for use in hypersonic vehicles and other extreme environments. Photo by Sam O’Keefe
Through the Enabling Materials for Extreme Environments signature area, Bill Fahrenholtz and Greg Hilmas are testing the thermal and mechanical properties of ceramics to find out what makes them stronger. They are investigating ultra-high-temperature materials for a variety of applications, including clean energy production, advanced propulsion systems and hypersonic flight vehicles. We sat down with the two Curators’ Professors of ceramic engineering to learn more about their research.
The above video provides more information about the Enabling Materials for Extreme Environments signature area.
Tell us about extreme environments.
Fahrenholtz: We are interested in many different extremes – temperature, radiation environments like in nuclear applications or even extreme mechanical loads. Chemical reactivity as well.
You can’t weld ceramics, right?
Fahrenholtz: Well, we are. In plasma arc welding, the arc is like a continuous bolt of lightning running from your welding tool that generates enough heat to melt a material and fuse two pieces together. A ceramic material has to be electrically conductive or the arc won’t be stable enough to heat properly. If you don’t have the right thermal conductivity, you’ll thermal-shock your material into a bunch of little pieces instead of welding it.
Hilmas: In thermal shock, you change the temperature of a material too quickly. If you take a drinking glass out of a hot dishwasher and fill it with ice water, you’re cooling the inside too quickly, but you still have hot glass on the outside. You’ve created a stress distribution through the material that it doesn’t like. Basically you’re transferring more tensile stresses to the atoms in and around that stress and it breaks. When you do the reverse – when you heat a material too quickly – the result tends to be even worse.
How do you avoid thermal shock?
Hilmas: To weld ceramic material we preheat it to close to half of its melting temperature. If we try to just nail it with that lightning bolt of electricity that Dr. Fahrenholtz mentioned, it heats too quickly and cracks.
But why would you want to weld ceramics?
Hilmas: Ceramic are difficult to make complex shapes out of. They’re hard, so they have to be machined with a diamond cutting tool and that’s expensive. We’re making leading edges for hypersonic aircraft. In the old days, we would have taken a block of ceramic material and machined it into the shape we’re looking for. We’ve demonstrated that you can take two plates, put them together at the right angle and just weld the tip. We’re working on basic research here. It’s like where the steel industry was decades ago.
Fahrenholtz: It’s no different than steel, like Greg said. Some grades of steel alloys are specifically designed to be weldable and others are difficult or impossible to join that way. We just have to find the right combinations of ceramics with the characteristics we need. It’s all part of the research. This is a unique case. With the exception of glass, most ceramics aren’t designed to melt and resolidify. People usually don’t melt things like zirconium diboride that we’re working on because its melting temperature – 3,250 degrees Celsius – is just so high.
How can tiny ceramic tiles help stop thermal shock?
Hilmas: We’re refining technology developed when I was at the University of Michigan, but using zirconium diboride to make ultra-high-temperature ceramics using an architecture that looks like a ceramic tile floor. You want your ceramic tiles to be surrounded by a material with dramatically different properties – like the grout in a tile floor, only at the microscopic level. If you’ve dropped something heavy on a ceramic tile floor, you know that a crack usually stops at the grout. That’s because the grout is porous and naturally blunts cracks. It’s like what we’re doing with this. The cracks in our sample stop in a single cell – or tile. By creating this weaker cell boundary phase – the grout, if you will – cracks run to the cell boundary phase and stop. It provides better wear resistance and boosts fracture toughness, which boosts thermal shock resistance. Take a material with pretty poor thermal shock resistance like zirconium diboride, which usually can withstand an instantaneous temperature change of 400 degrees Celsius before it acts like the glass out of your dishwasher. Using the ceramic tile architecture, we can take that same material to 1,400 degrees Celsius instantaneously without a catastrophic break. We’re also looking at different architectures than the traditional tile floor, like spirals, that might be easier to process. We have patented this technology.
Fahrenholtz: We’re demonstrating that ceramic materials have useful properties at well over 2,000 degrees Celsius. We’re really laying the ground work for learning basic material properties.
This story was modified from an interview originally published in re:search, the university’s annual report on key research activities.
Technology available for licensing
U.S. Patent 8,715,803 titled Ceramic Welds, and a Method for Producing the Same, issued on May 6, 2014, and U.S. Patent 8,192,853 titled Method for Toughening Via the Production of Spiral Architectures Through Powder Loaded Polymeric Extrusion and Toughened Materials Formed Thereby, issued June 5, 2012, are available for licensing through the Missouri S&T Office of Technology Transfer and Economic Development. For more information on licensing contact Vera Anderson, Licensing and Patent Associate, at 573-341-7263 or email vera@mst.edu.
Story by Mary Helen Stoltz
Photos by Sam O’Keefe
Video by Terry Barner
Recent Comments